LEAN Manufacturing kan echt een revolutie betekenen voor jouw bedrijf. Ga je er 100% voor, dan verandert niet alleen hoe jij werkt, maar ook hoe collega’s in productie, intralogistiek hun dagelijkse taken uitvoeren.
Sommigen noemen LEAN een verbetermethode, anderen een managementfilosofie of productiesysteem. Eigenlijk is het dat allemaal tegelijk: een slimme manier van werken met principes, technieken en een systematische aanpak. Zoals “The Toyota Way 2001” het mooi samenvat: ‘LEAN is een geïntegreerd socio-technisch systeem’.
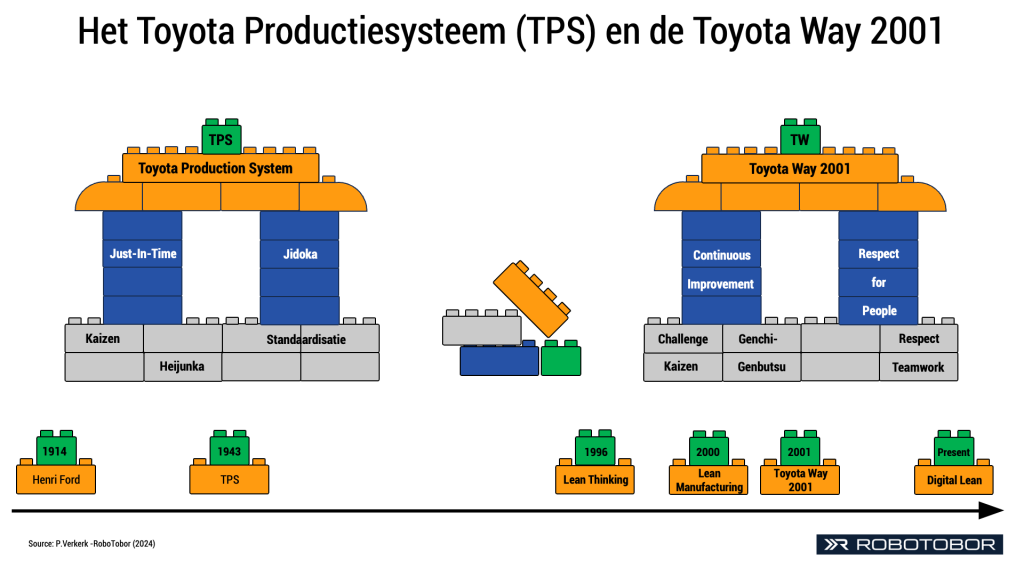
De wortels van LEAN liggen bij Henry Ford, werden verder uitgewerkt in het Toyota Production System (TPS) en vormden de basis voor LEAN Thinking. Later groeide dit door tot LEAN Manufacturing. Womack en Jones (1996) hebben LEAN Thinking naar LEAN Manufacturing vertaald met vijf kernprincipes:
- Value (waarde)
- Value Stream (de waardestroom)
- FLOW (Stroom)
- Pull
- Perfectie
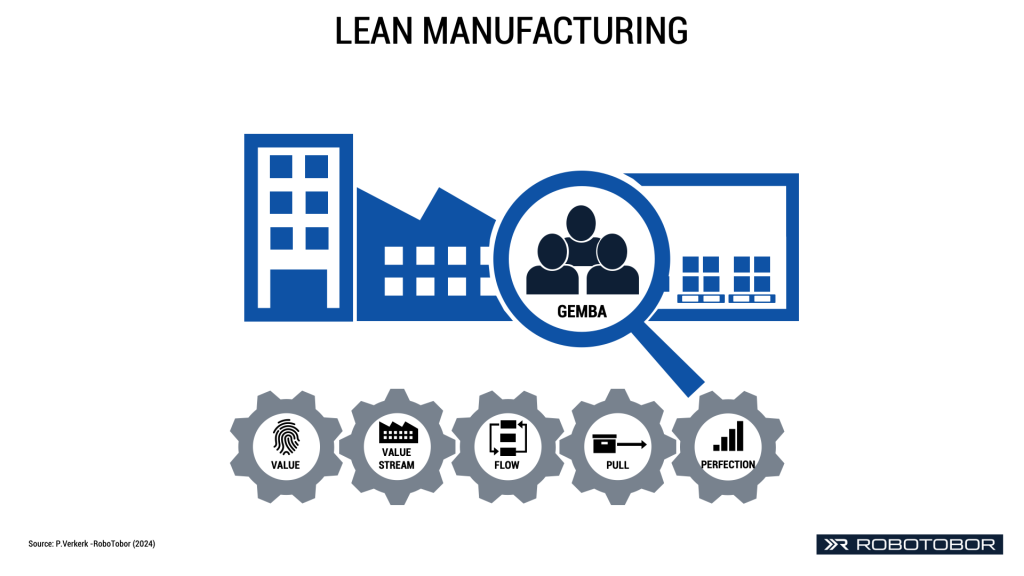
1. Value – ‘Waardecreatie en Klantgerichtheid’
Het principe van waardecreatie benadrukt het belang van het definiëren van specifieke kenmerken voor een product of dienst, gebaseerd op wat de klant bereid is te betalen. Het focust op het begrijpen van klantwaarden en het leveren van producten of diensten die aan hun behoeften en verwachtingen voldoen. Activiteiten die niet bijdragen aan deze waarde worden als overbodig (afval of Muda) beschouwd en moeten worden geëlimineerd. Het doel is waarde te creëren vanuit het klantperspectief door verspilling en kosten te verminderen, wat resulteert in de optimale prijs voor de klant en gemaximaliseerde winst. Het elimineren van muda uit het productie- of intralogistieke proces is een belangrijke eerste stap in waardecreatie. Afval heeft een aanzienlijke invloed op de prestaties van de organisatie en vermindert de winst.
2. De Value Stream – ‘Optimaliseren van Productieprocessen met LEAN Manufacturing’.
Het value stream-principe richt zich op het elimineren van niet-waarde toevoegende activiteiten en het behouden van processen die waarde creëren. Door materialen en hulpbronnen in de productlevenscyclus te analyseren, verminder je verspilling. Alle activiteiten in een organisatie vallen in drie categorieën:
- waarde toevoegend
- niet-waarde toevoegend
- noodzakelijk
Met ‘Value Stream Mapping’ krijg je snel inzicht in de huidige en gewenste toestand van je productieorganisatie. Een waardestroom omvat alle stappen die een product doorloopt via essentiële materiaal- en informatiestromen. Het doel is verspilling te elimineren en waarde toe te voegen.
Met deze 4 stappen verbeter je processen, stroomlijn je activiteiten en versterk je je concurrentiepositie:
Stap 1: Visie, doel en afbakening
Stap 2: Huidige waardestroom in kaart
Stap 3: Toekomstige waardestroom ontwerpen
Stap 4: Implementatie en continue verbetering
Heb je net een Value Stream Mapping (VSM)-sessie achter de rug? Misschien kwam in stap 4 naar voren dat je je productie-layout wilt optimaliseren. Lees dan eens over Systematische Layout Planning (SLP).
Hulp nodig met robotisering?
De stap naar robotisering kan overweldigend zijn, daarom sta ik klaar om jou te helpen!
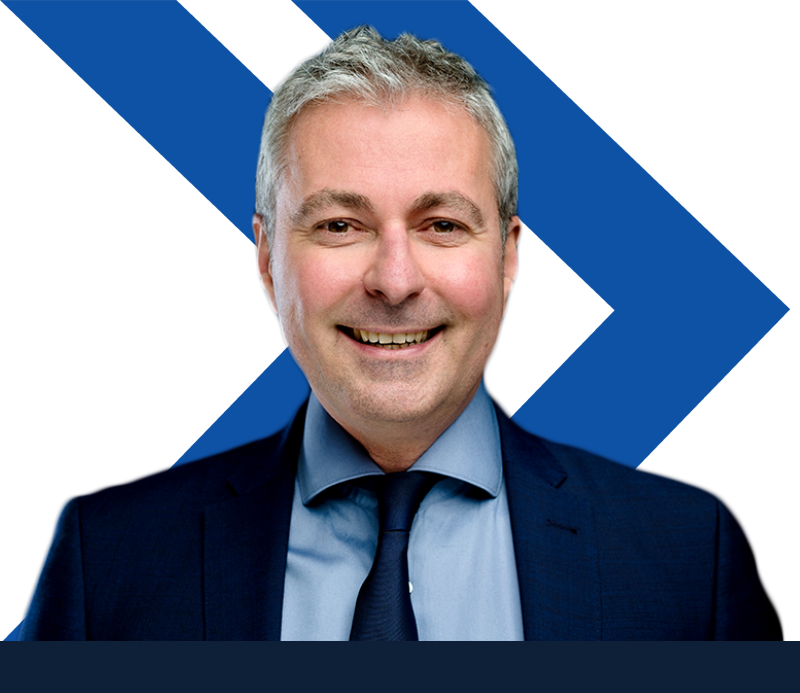
3. Flow: ‘Optimalisatie van de operationele FLOW’
Het creëren van ‘FLOW’ in bijvoorbeeld je intralogistiek betekent het zo organiseren van alle activiteiten dat ze continu en vloeiend plaatsvinden, zonder verspilling. FLOW verwijst naar de opeenvolgende stappen die waarde toevoegen aan een product en streeft naar een ononderbroken materiaalstroom. Door knelpunten en onderbrekingen te elimineren, verlopen activiteiten sneller en efficiënter, wat resulteert in verkorte cyclustijden en een vergroot reactievermogen. Onderbroken en disharmonische productieprocessen brengen kosten met zich mee, terwijl het streven naar FLOW leidt tot een constante productie of dienstverlening en resulteert in kostenvermindering.
Productie optimalisatie met LEAN Manufacturing
Wat was het probleem:
Het productieproces van een beddenfabriek, bestaande uit robot laslijnen, een spuiterij en een assemblage afdeling, voldeed niet aan de verwachtingen. De output was inconsistent, en de assemblage kende grote fluctuaties in werkdruk. Soms was er te weinig werk voor de medewerkers, dan weer te veel. Dit leidde tot inefficiënties en onregelmatigheden.Hoe verliep het onderzoek en de uitvoering:
Om deze problemen aan te pakken, implementeerde de onderneming methoden uit LEAN Manufacturing. Ze voerden een Pull-systeem in, ook wel ‘Make-to-Order’ genoemd, waarbij de productie pas start na ontvangst van een klantorder. Alleen standaardonderdelen en grondstoffen liggen op voorraad. Ze pasten ook het Heijunka-principe toe om de productievolgorde te balanceren en pieken en dalen in de procestijden op te vangen. Daarnaast werden de prioriteitsregels in de spuiterij aangepast om de output te verbeteren. Een simulatiemodel werd gebruikt om de prestaties van het productieproces te evalueren en optimaliseren.Wat was het resultaat:
Deze LEAN aanpak verminderde de fluctuaties in werkdruk en verhoogde de efficiëntie. De korte levertijd van twee weken bleef gehandhaafd, en de productie is beter afgestemd op de klantvraag. Hierdoor is een stabiel productieproces gerealiseerd, waarbij de output voldoet aan de verwachte kwaliteit en kwantiteit.
Magazijn optimalisatie met LEAN Manufacturing
Wat was het probleem:
Een productiebedrijf dat dak-producten voor de bouwindustrie vervaardigt, kampte met lange afhandelingstijden door verkeersknelpunten, eenrichtingsverkeer, verouderde werkmethodes en een inefficiënte magazijnindeling. Deze problemen veroorzaakten transportinefficiënties en verminderden de productiviteit.Hoe verliep het onderzoek en de uitvoering:
Voor het onderzoek werden diverse LEAN Manufacturing-methoden toegepast, zoals Spaghettidiagrammen, Value Stream Mapping en Time Value Mapping. De analyse toonde aan dat een aanzienlijk deel van de tijd niet bijdroeg aan de waarde van de producten: ongeveer 66% voor product 1 en 11% voor product 2, vooral door inefficiënt transport. Dit benadrukte dat transport de grootste oorzaak van tijdsverspilling was. Om deze problemen aan te pakken, werden drie oplossingen voorgesteld: het inzetten van Automatisch Geleide Voertuigen (AGV’s) om het intern transport te optimaliseren, het upgraden van de deuren en het optimaliseren van de magazijnindeling door snellopende producten dichter bij de magazijn in/ uitgang te plaatsen, rekening houdend met ruimtebeperkingen en de FIFO-methodologie.Wat was het resultaat:
De implementatie van deze maatregelen resulteerde in een aanzienlijke verbetering van de afhandelingstijden en de efficiëntie van de logistieke afdeling. Het interne transport werd gestroomlijnd met AGVs, wachttijden werden verminderd en de productiecapaciteit werd beter voorbereid op toekomstige groei.
4. Pull: “Pull-Productie en Just-in-Time”
LEAN pleit voor Just-In-Time (JIT) productie, waarbij de productie pas start bij daadwerkelijke klantvraag, om overproductie en overtollige voorraad te vermijden. Dit staat in contrast met push-systemen, die vooraf voorraden bepalen op basis van voorspellingen, wat vaak leidt tot inefficiënties en klanttevredenheidsproblemen. Een pull-systeem reageert alleen op vraag, vereist flexibiliteit en efficiënte processen voor succes. Just-in-time minimaliseert de voorraad en zorgt dat producten precies op tijd worden gemaakt. KAIZEN bevordert dit door een cultuur van continue verbetering, die afval vermindert, productiviteit verhoogt en innovatie stimuleert. De KAIZEN-methodologie is gebaseerd op vijf kernprincipes voor continue verbetering.
5. Perfectie: “Streven naar Perfectie”
Het streven naar perfectie is het kernprincipe van LEAN, waarbij continue verbetering centraal staat. Dit houdt in dat alle medewerkers op alle hiërarchische niveaus betrokken zijn bij het identificeren van problemen en het aandragen van oplossingen om processen en operationele efficiëntie te optimaliseren. Deze zoektocht naar perfectie, ook wel ‘KAIZEN’ genoemd, vereist voortdurende beoordeling en verbetering van processen om verspilling te elimineren en het ideale systeem voor de “waardestroom (FLOW)” te vinden. Om dit in de organisatiecultuur te integreren, zijn metingen zoals doorlooptijden en productiecycli essentieel.
Ben je benieuwd naar mijn manier van werken? Kijk dan eens naar mijn Totaalaanpak voor maakbedrijven warehouses en ziekenhuizen of de LMTRF-methode voor robot integratoren en machinebouwers.
Copyright © 2024; Patrick Verkerk, RoboTobor