De opkomst van Digital Twins: Van handmatige expertise naar digitale expertise
Vroeger, voordat machines onderling konden communiceren en voordat Industrie 4.0 en het Internet of Things (IoT) opkwamen, hadden productieomgevingen toegewijde medewerkers. Deze mensen kenden alles over machines, producten en het productieproces. Ze waren het aanspreekpunt, hielden een oogje in het zeil, volgden planningen en voorkwamen problemen. Deze experts vormden de schakel tussen complexe productie-informatie en de praktijk, gebaseerd op hun kennis en ervaring.
Met de groeiende digitalisering en complexiteit van productieomgevingen wordt het steeds moeilijker voor medewerkers om alles goed te begrijpen. De overvloed aan complexe en onderling verbonden gegevens vraagt om systemen die gegevens helder kunnen interpreteren en presenteren. Dit geldt voor alle vakgebieden, maar vooral in de industrie en intralogistiek waar nieuwe technologieën snel worden omarmd.
Digital Twins, oftewel digitale kopieën van producten, processen of systemen, bieden enorme voordelen, vooral binnen Industrie 4.0. Deze technologie maakt het ordenen van complexe gegevens en systemen eenvoudiger, waardoor mensen informatie gemakkelijker kunnen bekijken, begrijpen en zelfs voorspellen. Het gebruik van Digital Twin-technologieën verbetert de productiviteit, verhoogt de productkwaliteit, biedt meer flexibiliteit en helpt tegelijkertijd kosten te verlagen.
Vroeger was toegang tot Digital Twin-technologie vaak beperkt vanwege hoge kosten voor computergebruik, opslag en bandbreedte. Maar in de afgelopen jaren zijn deze obstakels aanzienlijk verminderd, met lagere kosten en betere capaciteiten als resultaat. Dit heeft geleid tot belangrijke veranderingen, waardoor Informatietechnologie (IT) en operationele technologie (OT) nu eenvoudig kunnen worden gecombineerd om Digital Twins te creëren en toe te passen.
Wetenschappelijke definities van een Digital Twin (DT)
Binnen de wetenschappelijke definities van een Digital Twin (DT) zijn diverse omschrijvingen te vinden:
Van relatief eenvoudige omschrijvingen:
“Een Digital Twin (DT) is een model van een fysiek systeem dat het fysieke systeem in realtime weerspiegelt en analyse, voorspelling en controle mogelijk maakt.
“Een Digital Twin (DT) is het conglomeraat van gegevens, informatie, modellen, methoden, hulpmiddelen en technieken om de huidige toestanden van een geïnstantieerd systeem op coherente en consistente wijze weer te geven”
Tot meer complexe omschrijvingen:
“Een Digital Twin (DT) is een virtuele representatie van een fysiek object of systeem dat is ontworpen, gebouwd en in operatie in een digitale omgeving. Deze digitale replica kan gedetailleerde informatie bevatten over de fysieke kenmerken, het gedrag en de prestaties van het object of systeem in de echte wereld” Digitale tweelingen worden gebruikt in verschillende sectoren om de prestaties van fysieke entiteiten te monitoren, analyseren en optimaliseren”.
“Een Digital Twin (DT) is een geïntegreerde multi-fysische, multidimensionale probabilistische simulatie van een complex fenomeen of product, waarbij gebruik wordt gemaakt van de best beschikbare fysieke modellen, sensorische interfaces, wiskundige kennis om een spiegel te creëren van het bestaan van de bijbehorende tweeling. Het bestaan van een digitale tweeling wordt bepaald door drie componenten, namelijk: het bestaan van een reëel fysiek element, een virtueel element en een set gegevens die een link vormen tussen een materieel (echt) element of product en een virtueel element”.
De geschiedenis van Digital Twins
De geschiedenis van Digital Twins begon in de jaren zestig, toen NASA het concept introduceerde als een ‘levend model’ voor de Apollo-missie, na het incident met de zuurstoftank van Apollo 13. NASA combineerde fysieke modellen met digitale elementen om voortdurend gegevens te verzamelen, wat cruciaal was voor het onderzoek naar ongelukken en het begrip ervan.
In 2002 werd de Digital Twin voor het eerst aan de industrie gepresenteerd aan de Universiteit van Michigan als onderdeel van het ‘Product Lifecycle Management (PLM)’ centrum. De presentatie, ontwikkeld door Dr. Grieves, was getiteld ‘Conceptueel Ideaal voor PLM’ en bevatte alle elementen die nu geassocieerd worden met de Digital Twin.
In de jaren tachtig verschenen 2D CAD-systemen zoals AutoCAD, waarmee technische tekeningen op de computer konden worden gemaakt. CAD evolueerde naar 3D met parametrische modellering en simulatie, waardoor intelligent ontwerpen van complexe assemblages mogelijk werd. In het midden van de jaren 2010 lanceerden toonaangevende 3D CAD-leveranciers Cloud gebaseerde oplossingen, in eerste instantie gericht op samenwerking en projectbeheer, later ook op generatief ontwerp.
De huidige tijd markeert het tijdperk van realtime 3D-aangedreven Digital Twins (DT), virtuele representaties van processen, systemen, werknemers, gegevens of de hele omgeving. Ze fungeren als dynamische dragers van data en statusinformatie verkregen via sensoren die verbonden zijn door het Internet of Things (IoT).
Hier zijn de 5 stappen om te beginnen met Digital Twin-technologie:
Stap 1: Bepaal het startpunt: gegevensuitwisseling
Stap 2: Kies het type Digital Twin: product, systeem/proces of multisysteem
Stap 3: Bepaal het gebruik en doel van een Digital Twin applicatie
Stap 4: Leer van bestaande Digital Twin-toepassingen
Stap 5: 6 belangrijke aandachtspunten voor een succesvolle implementatie
Stap 1: Bepaal het startpunt: gegevensuitwisseling
Digital Twins kunnen worden onderscheiden op basis van de richting van de datastroom (gegevensuitwisseling) en hun beoogde toepassing. Ze fungeren allemaal als digitale representaties van fysieke objecten of producten. Digital Twin (DT), Digital Shadow (DS) en Digital Model (DM) verschillen in capaciteiten, waarbij DT als het meest geavanceerd wordt beschouwd.
1.Digital Model (DM):
Een Digital Model is simpelweg een 3D-kopie van een echt object of product. Er is geen automatische uitwisseling van gegevens tussen het fysieke en digitale model; alle wijzigingen moeten handmatig worden doorgevoerd. Veranderingen in het echte object hebben geen directe invloed op het digitale model, en omgekeerd.
2.Digital Shadow (DS):
Een Digital Shadow ontstaat aan het begin van de levenscyclus van een product, direct na het ontwerpproces, en creëert een virtuele weergave in de digitale wereld. Beschikbare gegevens omvatten ontwerp-, productie-, onderhouds- en gebruiksgegevens. Een DS ontvangt alleen gegevens van het fysieke object of product naar de digitale schaduw, zonder verstoring van de digitale schaduw door veranderingen in het fysieke object. De Digital Shadow kan alleen worden bijgewerkt door synchronisatie met de echte wereld.
3.Digital Twin (DT):
Een Digital Twin is een digitale kopie van een fysiek object, systeem of proces. Wat het onderscheidt, is een constante tweezijdige gegevensstroom tussen het fysieke object en het digitale. Deze volledig geïntegreerde stroom definieert een Digital Twin. Het reflecteert de echte wereld en wordt gebruikt voor het monitoren, analyseren, simuleren en voorspellen van de prestaties en het gedrag van het fysieke object.
Stap 2: Het type Digital Twin: een product of systeem/proces of multisysteem
Door technologische vooruitgang zijn verschillende soorten Digital Twins ontwikkeld, die specifieke aspecten van een product of systeem belichten. Dit omvat de Product Digital Twin, Systeem/Proces Digital Twin en MultiSysteem Digital Twin. De Product Digital Twin richt zich op prestaties en kwaliteit, terwijl de Proces Digital Twin gedetailleerd inzicht biedt en processen optimaliseert. Op het meest uitgebreide niveau staat de Systeem Digital Twin.
1. Product Digital Twin
Een Product Digital Twin is een digitale kopie van een onderdeel of het gehele product, zoals een mobiele robot of machine. Gedurende de levenscyclus worden gegevens verzameld over het ontwerp, de fabricage en de operationele processen. Door data-analyse kunnen prestaties worden gevolgd, onderhoud voorspeld en productontwerp geoptimaliseerd. Het helpt zelfs om foutieve gegevens op te sporen. Een Product Digital Twin verbetert de productkwaliteit van ontwerp tot onderhoud en preventief onderhoud, vermindert downtime en zorgt voor een betere klantervaring.
2. Systeem of Proces Digital Twin
Een AGV-systeem of robotapplicatie zijn voorbeelden van een Proces Digital Twin in een productieomgeving. IoT-gegevens worden in realtime gemonitord, processen worden gesimuleerd en geanalyseerd. Dit helpt bij het identificeren van problemen en het nemen van betere beslissingen. Het geeft een gedetailleerd inzicht in de interactie tussen verschillende onderdelen en hun impact op de algehele prestaties. Een Proces Digital Twin kan een volledige productielijn nabootsen, waarmee je knelpunten kunt identificeren, workflow kunt optimaliseren en de efficiëntie kunt verbeteren.
3. Multisysteem of Proces Digital Twin:
Een System Digital Twin ontstaat door verschillende Product- en Proces-Twins te combineren. Het omvat een volledig ecosysteem of netwerk, zoals een complete fabriek of magazijn. Hiermee kunnen we ingewikkelde lay-outwijzigingen, zoals die van AMR-systemen, materiaalstromen en machineaanpassingen, optimaliseren door middel van analyse en simulatie van gegevens. De inzichten die hier worden verkregen, zijn veelomvattend omdat ze de bredere impact van situaties op het hele systeem of de sector begrijpelijk maken. Dit niveau van Digital Twin-toepassing biedt organisaties een holistisch begrip, waardoor ze kunnen anticiperen op trends, risico’s kunnen minimaliseren en proactief kunnen innoveren. Bovendien helpt het bij het optimaliseren en toewijzen van middelen en het nemen van strategische beslissingen.
Stap 3: Bepaal het gebruik en doel van een Digital Twin applicatie
Met meer dan 210 Digital Twin applicaties kan het lastig zijn om het overzicht te behouden. Het XYZ Digital Twin Model biedt verheldering en ‘aha’-momenten. Voordat je begint met een Digital Twin (DT), doorloop je twee belangrijke fasen: Product Lifecycle Management (PLM) en de digitalisering van producten en machines (IoT). Het is verstandig om stapsgewijs te werk te gaan. Start met een belangrijk onderdeel of proces en schaal geleidelijk op naar een complete Digital Twin (DT). Om dit stapsgewijze proces te bepalen, kun je gebruikmaken van een model met 3 hoofddimensies.
Elke as vertegenwoordigt een dimensie van de Digital Twin:
1.De X-as: zes fasen van de productlevenscyclus: Ontwerp – Bouw – Operationeel – Optimaliseren – Onderhoud – Afdanken.
2.De Y-as: zes hiërarchische niveaus van een Digital Twin: van informatie tot multisystemen.
3.De Z-as: het gebruik of doel van de zeven meest voorkomende Digital Twin toepassingen, zoals simulatie of voorspellingen.
Er zijn minimaal 210 (5 x 6 x 7 = 210) verschillende Digital Twin combinaties mogelijk.
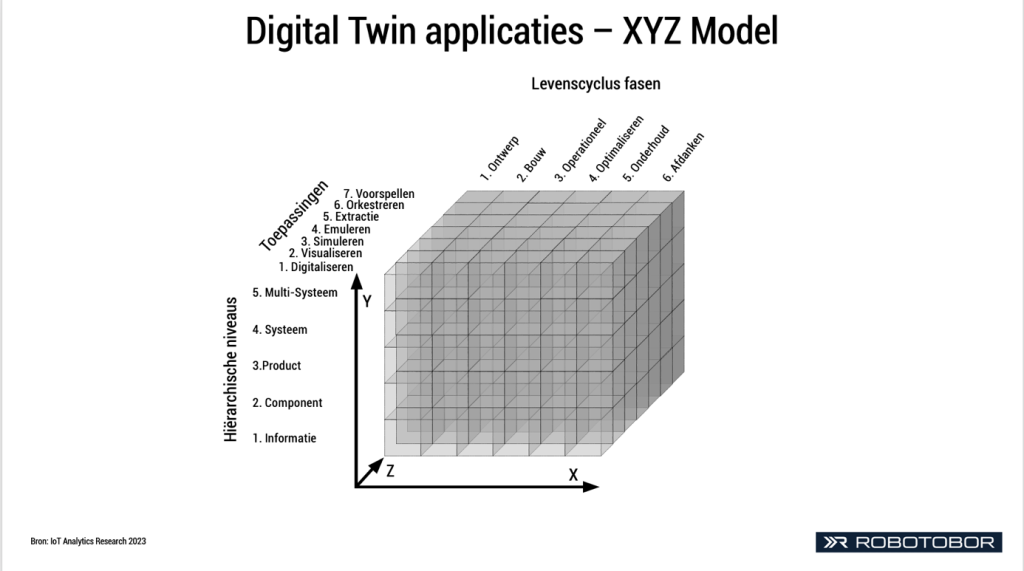
De kosten en complexiteit stijgen bij de overstap van een statische Digital Twin (DT) naar een dynamische Digital Twin (DT). Een cruciaal aspect in het 3D-model is de uitwisseling van gegevensstromen. Laten we nog eens kijken naar de Digital Model (DM), Digital Shadow (DS) en Digital Twin (DT). De Digital Shadow (DS) heeft in één richting een gegevensstroom, van het fysieke object naar de digitale schaduw, wat nog vrij statisch is. De uitwisseling van gegevens van een ‘Product Digital Twin’ wordt gekenmerkt door een constante tweezijdige gegevensstroom tussen het fysieke en digitale, wat dynamisch is. Bij het kiezen van een onderdeel op de Y-as, kun je rekening houden met de gegevensstroomuitwisseling: geen, historisch, test- of realtime gegevens.
Stel je voor dat je een robotcel bouwt. Je begint met een Digital Model (DM) van een machine die later in een productielijn van je klant wordt geïnstalleerd:
1.Ontwerp – grijs: Dit is de eerste fase van de productlevenscyclus. Alle CAD-ontwerpgegevens worden verzameld om een eenvoudige Digital Twin te maken. Op dit moment is het een Digital Model (DM), kosteneffectief maar met beperkte informatie.
2.Bouw – oranje: Tijdens de bouw worden fabricagegegevens verzameld, zoals een stuklijst met huidige en historische componenten, serienummers en uitgevoerde bewerkingen. Testen en metingen worden gedaan met behulp van IoT-sensoren. Dit verrijkt de beschikbare informatie. Nu is het een Digital Shadow (DS).
3. Operationeel – blauw: Na levering aan de klant worden operationele gegevens verzameld via IoT-sensoren in het product. Dit zorgt voor een live versie van het product bij de klant, wat diepgaande context en inzichten biedt. Deze fase is complexer en duurder. Nu is het een Digital Twin (DT).
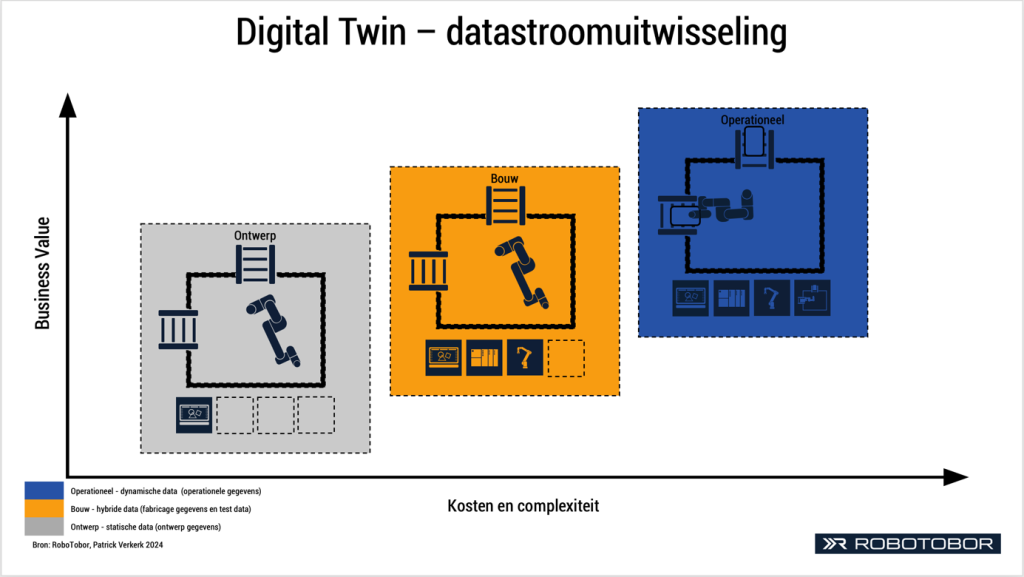
Hulp nodig met robotisering?
De stap naar robotisering kan overweldigend zijn, daarom sta ik klaar om jou te helpen!
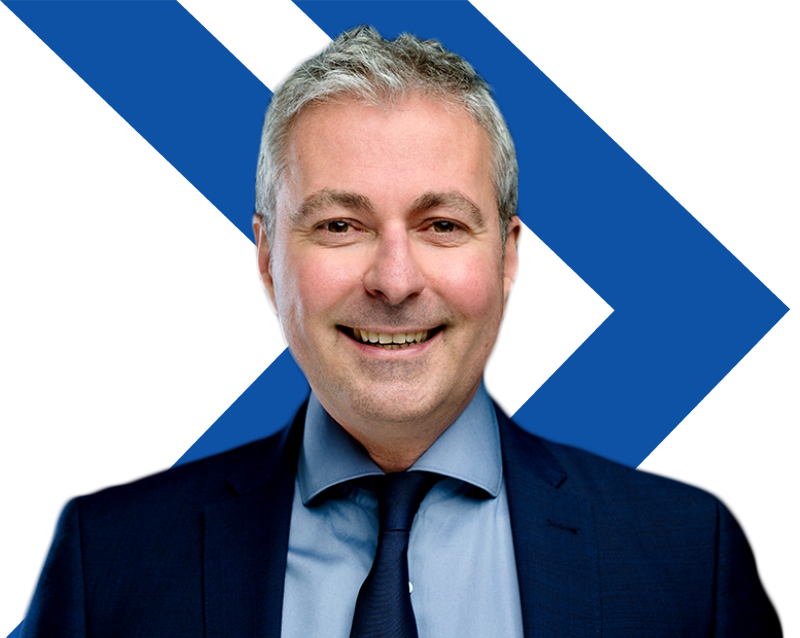
Stap 4: Leer van bestaande Digital Twin toepassingen
Zes veelvoorkomende toepassingen van Digital Twins (bron: IoT Analytics) zijn:
- Systeem voorspellingen;
- Systeem Simulatie;
- Asset interoperability;
- Onderhoud;
- Systeem Visualisatie;
- Product simulatie.
1. Systeemvoorspellingen: Deze Digital Twin-toepassingen richten zich op het voorspellen van het gedrag en de toekomstige toestand van complete systemen, zoals een deel of het geheel van een fabriek, gebouw of machine. Ze optimaliseren de levenscyclusfase door gebruik te maken van actuele en historische gegevens. De kern van deze Digital Twins bestaat uit modellen die worden gebruikt om toekomstige resultaten te voorspellen.
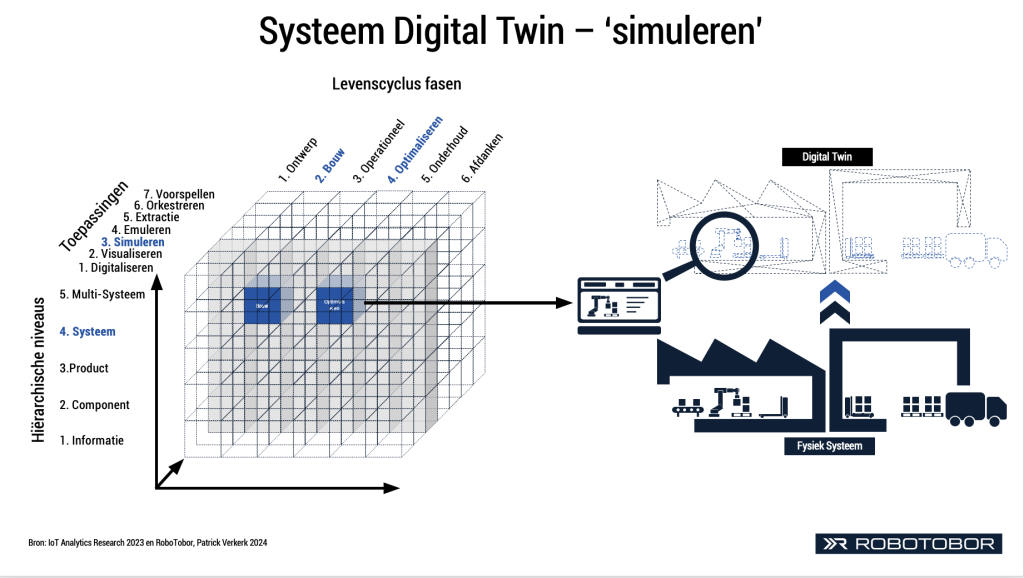
2. Systeemsimulatie: Tijdens de ‘Bouw’ en ‘Optimaliseren’-fasen van de levenscyclus worden systeemsimulaties gebruikt. Deze simuleren grote, complexe systemen met vele variabelen door middel van ‘wat-als’-scenario’s. Denk aan een volledig magazijn met robotarmen die producten op pallets stapelen in specifieke volgordes, terwijl mobiele robots deze pallets oppakken en verplaatsen naar verschillende locaties in het magazijn. Veranderingen in de lay-out, robots of materiaalstromen beïnvloeden het systeemontwerp en de prestaties. Belangrijke voordelen van deze simulaties zijn het valideren van concepten en het verminderen van kosten.
3. Asset interoperabiliteit: Tijdens de ‘Operationeel‘ of ‘Optimaliseren’-fasen van de levenscyclus worden gegevens uit verschillende bronnen verzameld, geïntegreerd en geanalyseerd om meer data gestuurde beslissingen mogelijk te maken. Met de groei van IoT-sensoren neemt het volume en de complexiteit van gegevens jaarlijks toe. Dit kan bijvoorbeeld worden toegepast op een AMR voertuig, waarbij ruwe sensorgegevens worden verzameld en gemodelleerd tot een Digital Twin-applicatie. Deze Digital Twin vertegenwoordigt de gegevens aan de hand van real-world concepten die ingenieurs begrijpen.
4. Onderhoud: Een maintenance Digital Twin-applicatie ondersteunt tijdens de ‘onderhoud’ fase van de levenscyclus, vaak met inbegrip van ‘voorspelling’. Het hoofddoel is het waarborgen van de operationele effectiviteit van het systeem. Het onderhoudspersoneel ontvangt gedetailleerde informatie tijdens een geplande downtime of over reparatietaken. Deze applicaties maken voorspellend onderhoud mogelijk door gebruiksscenario’s, waardoor kostbare stilstanden worden voorkomen.
5. Systeemvisualisatie: Tijdens de ‘operationeel’ levenscyclusfase wordt de Digital Twin-applicatie gebruikt om een systeem of machine te visualiseren. Een veelgebruikte vorm van visualisatie zijn 3D-elementen, vaak gegenereerd met CAD-tekeningen, die helpen bij het verbeteren van de transparantie over de actuele operationele status van het systeem. De applicatie maakt gebruik van gegevens uit productie of magazijn, zoals IoT-gegevens van camera’s, GPS-ontvangers en RTLS. Deze gegevens worden ingezet om met geavanceerde machine learing algoritmen een interactieve 3D-replica van de lay-out te creëren. Dit helpt het personeel om de veiligheid te verhogen en de prestaties te verbeteren, vaak inclusief ‘simuleren’.
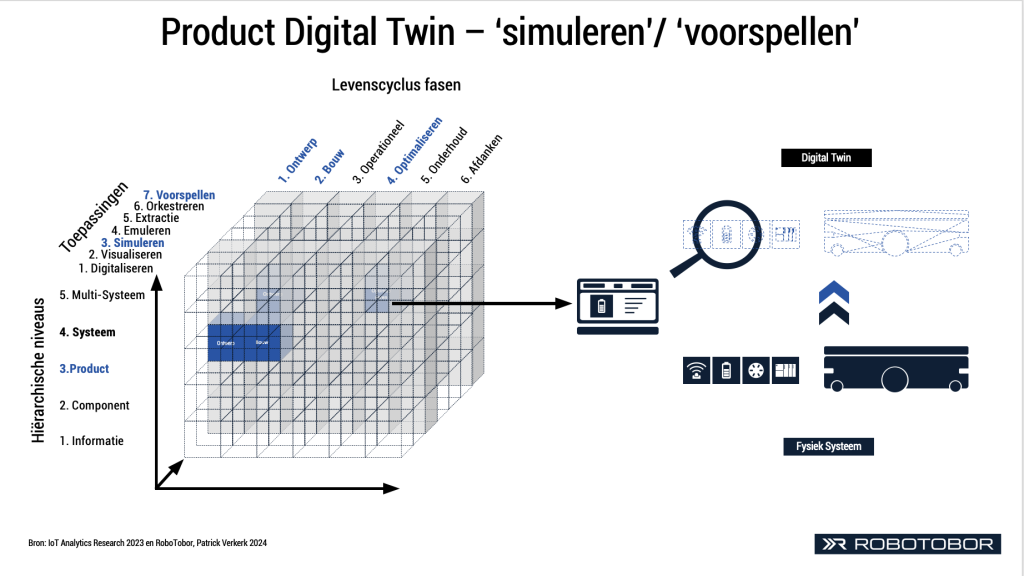
6. Product simuleren/voorspellen: Tijdens de ‘Ontwerp’ of ‘Bouw’-fase maken Digital Twin-applicaties gebruik van productsimulatie, wat de basis legt voor de ontwikkeling van nieuwe en verbeterde producten. Een cruciale toepassing is het simuleren van diverse ontwerpen voor een toekomstig product vóór productie en assemblage. Hierdoor worden kostbare prototypes overbodig en kunnen snel duizenden productvarianten worden getest. Digital Twin-applicaties zijn nauw verbonden met engineering- en ontwerpsoftware. Binnen het ‘voorspellen’ wordt geanalyseerd hoe hoge en lage toleranties het gedrag van het ontworpen product beïnvloeden.
Wat is het verschil tussen simulatie software en een Digital Twin software?
Systeem ‘voorspellen‘ en systeem ‘simuleren’ winnen aan populariteit, met steeds meer klanten die deze technologieën omarmen. Het is belangrijk om het concept van een Digital Twin te onderscheiden van een eenvoudige 2D of 3D-simulatie. In een simulatie wordt een scenario gecreëerd van mogelijke gebeurtenissen onder specifieke omstandigheden. Een Digital Twin-applicatie daarentegen vertegenwoordigt realtime gebeurtenissen in een machine of proces, mogelijk gemaakt door de voortdurende uitwisseling van gegevens tussen de echte en virtuele ruimte.
Andere of toekomstige Digital Twin-toepassingen omvatten:
-DT-trainingen met Extended Reality (XR) gebaseerd op Augmented Reality (AR), Virtual Reality (VR) en Mixed Reality (MR)
-DT realtime machinecontrole met AI-algoritmen
-DT voor gezondheidsvoorspellingen van sensoren, motoren, actuatoren en robots
-DT geïntegreerd met Lean Manufacturing principes en tools zoals Kanban
-DT in combinatie met 3D realtime Marketing
Digital Twin-applicaties variëren afhankelijk van de levenscyclusfase en het gebruik van een product. Met meer dan 210 mogelijke toepassingen gedurende de volledige levensduur van een product, kunnen Digital Twin-toepassingen realtime vragen beantwoorden die voorheen onmogelijk waren. Deze technologie heeft een positieve impact op complete industrieën door verbeteringen te realiseren in productie-efficiëntie, systeemdowntime te verminderen en veiligheid en winstgevendheid te verbeteren.
Stap 5: 6 aandachtspunten voor een succesvolle Digital Twin-implementatie
Het ontwikkelen van betaalbare producten, systemen en diensten vereist hoogproductieve technische teams die topkwaliteit kunnen leveren. Digital Twin-oplossingen maken gebruik van gegevens uit diverse bronnen, zoals IoT-sensoren, CAD-modellen en historische en realtime gegevens, opgeslagen in verschillende formaten en systemen. Het integreren van deze gegevens in één model is complex en uitdagend, en vereist zorgvuldige planning om de juistheid en volledigheid van de gegevens te waarborgen. Uitdagingen kunnen ontstaan door verouderde IT-infrastructuur, gegevensbeveiliging en het ontbreken van een gestandaardiseerde modelleringsaanpak.
De creatie van een Digital Twin-model omvat verschillende fasen, zoals dynamische dataverzameling van mobiele sensoren, datacommunicatie, realtime datasimulatie en -modellering, machine learning en data-analyse, visualisatie en business intelligence, en beveiliging. Het opzetten van een Digital Twin is vaak een iteratief proces dat evaluatie en aanpassingen vereist, volgens het Plan-Do-Check-Act-principe.
De 6 belangrijkste aandachtspunten voor een succesvolle implementatie van een Digital Twin-project zijn:
1. Plan – Beginnen met Digital Twin Planning
Een Digital Twin-plan begint met een duidelijke link tussen bedrijfsstrategie en doelstellingen. Begin met een brainstormsessie om mogelijke Digital Twin-toepassingen te identificeren (er zijn minstens 210 mogelijkheden). Maak daarna een shortlist met prioriteit voor scenario’s die snel winst opleveren en probleemgebieden blootleggen. Een Digital Twin kan zo simpel of complex zijn als nodig, afhankelijk van de benodigde gegevensnauwkeurigheid. Kies een Digital Twin-type, uit het Digital Twin-applicaties XYZ Model, dat past bij de groeifase van je bedrijf en binnen het budget. RoboTobor biedt zes ontwikkelstappen voor krachtige Digital Twin-oplossingen in material-handling en intralogistiek: Visualiseren; Identificeren; Pilot; Ontwikkelen; Opschalen; Monitoren.
2. Kennisopbouw – Creëer een expertisecentrum
Bedrijfs- en IoT-gegevens zijn vaak verspreid over verschillende bronnen zoals databases, spreadsheets en modellen (CAD, BIM, GIS). Betrek collega’s met expertise (domein kennis) en bouw voort op bestaande IoT-sensoren. Stel een multidisciplinair team samen met expertise in data science, toegepaste wiskunde en techniek. Een Data Scientist kan ongestructureerde en gestructureerde data verwerken voor gebruik in de Digital Twin. Vorm een intern en extern technologieteam dat geschikt is voor het gekozen IoT- en Digital Twin-platform.
3. Manage – Stakeholder- en projectmanagement
Zorg ervoor dat het management goed op de hoogte is en blijft van de Digital Twin-technologie en of het geïdentificeerde probleem wordt aangepakt. Zorg voor voortdurende updates over de status en voortgang van het project, gezien Digital Twin-projecten risico’s en tijd vergen.
4. Technologie – Partners en platforms
Maak het technologische ecosysteem helder met platform leveranciers en systeem integrators. Kies partners voor de benodigde functies en infrastructuur. Zorg ervoor dat een ervaren leverancier de technologie op maat kan maken voor de specifieke Digital Twin-toepassing. Manage zowel interne als externe projectteamleden.
5. Cultuur – Verandermanagement
Bereid de organisatie voor op verandering via training, interventies en beleid. Dit vergroot de geloofwaardigheid bij het implementeren van nieuwe werkprocessen en cultuur. Vaak stuiten leiders op een kloof tussen hun huidige en gewenste cultuur. Culturele ‘Enablers’ zijn cruciaal voor een innovatieprogramma zoals een ‘Digital Twin.’ Een cultuur van voortdurende verbetering, zoals bij Lean Manufacturing, vereist sterke betrokkenheid op de werkvloer, vooral van het management.
6. PDCA – Plan, Do, Check, Act: Acties en Evalueren
C is een controlepunt, vaak gericht op relevante KPI’s, zoals Productiviteit, Kwaliteit, Kosten, Levering, Veiligheid en Moraal (PKKLVM-structuur bij Lean Manufacturing). Het ‘Act’-gedeelte omvat alle projectacties en de hoofdoorzaken voor eventuele afwijkingen. Veel bedrijven zijn goed in plannen maar vinden het lastig om de prestaties te handhaven en snel passende maatregelen te nemen. Dat is de uitdaging. Evalueer de resultaten van de eerste proef of pilot, analyseer bedrijfsresultaten en voer iteraties uit voor groot succes.
Ondanks uitdagingen groeit Digital Twin technologie snel en wordt het steeds relevanter.
Het is niet meer de vraag óf je moet beginnen, maar waar je moet beginnen!
Cobot-, zes-assige articulated robot- of Delta robotsystemen zijn ideaal voor Digital Twin oplossingen. Zowel bestaande als nieuwe PLC’s verzamelen, registreren en verwerken signalen uit een robot of robotcel. Deze signalen kunnen worden verrijkt met procesinformatie van MES, ERP en WMS-systemen, waarbij OT en IT samenkomen. In de Systeem of Proces Digital Twin wordt de fysieke lay-out constant gesynchroniseerd met de digitale. Het hele proces van ontwerp tot productie kan worden gesimuleerd en geanalyseerd gedurende de productlevenscyclus.
De combinatie van Lean Manufacturing en Digital Twin-technologie vermindert verspillingen en kosten.
Copyright © 2024; Patrick Verkerk, RoboTobor