LEAN is HOT! De afgelopen jaren ben ik intensief bezig geweest met LEAN. Echter, Lean integreer je niet zomaar even in je productie organisatie. Net als bij andere technologieën, zoals een Warehouse Management Systeem (WMS), begint het met een grondig onderzoek. Je stelt jezelf de vraag wat precies nodig is voor een succesvolle integratie. En, wat levert het op? LEAN heeft een rijke geschiedenis, waarin Henry Ford en Toyota een centrale rol hebben gespeeld. Daarom start ik met een historische verkenning. Waarom? Veel LEAN (TPS) tools uit het verleden zijn nog steeds zeer relevant en hebben een blijvende impact.
6 redenen waarom je dit artikel moet lezen, omdat:
- Het begrip LEAN een opstap is naar LEAN Manufacturing.
- Je de twee belangrijkste LEAN hoofdpijlers, Just-In-Time (JIT) en de Jidoka moet begrijpen.
- Je voorraadniveaus & doorlooptijden kunt verminderen met Just-In-Time (JIT).
- LEAN een socio-technisch systeem is: investeer in mensen met “respect for people”.
- De ‘The Toyota Way’ nieuw leven inblaast in een vastgelopen LEAN-implementatie.
Technologie, zoals robots, maakt het mogelijk om repetitief en eentonig werk grotendeels te elimineren. Wil je dat dit effectief wordt geïntegreerd in je organisatie? Kies dan de juiste LEAN-tools om dit te ondersteunen. Twijfel je erover welke LEAN-tool het beste is voor jouw situatie? Ik sta klaar om je te helpen! Neem gerust contact op. Robot Start is als de ‘Lekker Makkelijk Strippenkaart’ – jouw gebruiksvriendelijke hulplijn op het moment dat het jou uitkomt.
De ontwikkeling van LEAN: Van Henry Ford tot Toyota
De basisprincipes van LEAN lijken al eeuwen te bestaan. In het begin van de 20e eeuw introduceerde Henry Ford de flowproductie met een lopende band voor de massaproductie van T-Fords. Deze werden vervaardigd volgens het “Push” principe, wat soms leidde tot ongewenste voorraden door te optimistische verkoopplanning. Het Ford-productiesysteem kende weinig variatie, aangezien het Model T slechts in één kleur beschikbaar was.
In het naoorlogse Japan ontwikkelde Toyota, onder leiding van Taiichi Ohno en Shigeo Shingo, het lopende band principe verder. Ohno, industrieel ingenieur en manager bij Toyota, concludeerde dat het verminderen of elimineren van verspilling de productie-efficiëntie verhoogt. Hij hechtte ook sterk aan de bijdragen van werknemers op alle niveaus en bedacht methoden om hun ideeën vast te leggen, zoals de zeven verspillingen (muda), Just-In-Time (JIT) manufacturing, Kanban, Jidoka, Supermarkten, Cellulaire productie, Takttijd en de Ohno-cirkel.
Samen met Shingo legde Ohno de basis voor het Toyota Productie Systeem (TPS), met de twee hoofdpijlers Just-In-Time (JIT) en Jidoka. JIT bevordert een soepele productieketen zonder overbodige voorraden, terwijl Jidoka problemen detecteert en de productie stopt om kwaliteitsdefecten te voorkomen. Het succes van TPS wordt toegeschreven aan een cultuur waarin problemen worden gezien als kansen voor verbetering, waarbij managers fungeren als coaches voor werknemers.
Het International Motor Vehicle Program (IMVP) van het Massachusetts Institute of Technology (MIT) speelde een cruciale rol bij het begrijpen van Lean Manufacturing (LM). De term “LEAN” werd in 1988 geïntroduceerd door John F. Krafcik en verder ontwikkeld door James Womack, Daniel T. Jones en Daniel Roos in hun boek ‘The Machine that Changed the World’ uit 1990. Womack en Jones definieerden de kernprincipes van LEAN in hun boek uit 1996, ‘LEAN Thinking: Banish Waste and Create Wealth in Your Corporation’. De kern van LEAN is het maximaliseren van klantwaarde terwijl verspilling wordt geminimaliseerd. De praktische toepassing van LEAN varieert, maar het wordt nu gezien als een continu traject voor organisatieverbetering.
Het Toyota Production System: De fundamenten van JIT en Jidoka
Het succes van Toyota komt door hun managementstijl, waar medewerkers worden aangemoedigd om voortdurend te streven naar verbetering (Kaizen) en hogere productkwaliteitsnormen na te streven. Deze Kaizen-initiatieven hebben geleid tot het Toyota Production System (TPS), met als centraal idee dat mensen gewaardeerd moeten worden. TPS rust op twee pijlers: Just-In-Time (JIT) en Jidoka, en deze staan op de Heijunka basis. TPS wordt wereldwijd geanalyseerd en geïmplementeerd om productie, werkplek, toeleveringsketen en interactie tussen leveranciers en klanten efficiënt te organiseren. TPS is gebaseerd op ‘Verminderen van verspilling’ en ‘Gestandaardiseerd werk’,
De 6 voordelen van Het Toyota Productie Systeem (TPS)
- Vermindert verspillingen
- Verbeterd productkwaliteit
- Vermindert het voorraadniveau
- Optimaliseert de fysieke ruimte
- Verbeterd de klant/ leverancier relatie
- Verbeterd het Teammoraal
Het Toyota Institute en De Toyota Way
In 2002 richtte Toyota het Toyota Institute op. De filosofie, principes en waarden van het Toyota Productiesysteem (TPS) werden gebundeld in ‘de Toyota Way 2001’. Dit systeem rust op twee pijlers: ‘Continu verbeteren’ en ‘Respect voor mensen’, ondersteund door vijf sleutelwoorden: ‘Challenge’, ‘Kaizen’, ‘Genchi Genbutsu’ (ga het zelf zien), ‘Respect’ en ‘Teamwerk’.
Auteur Jeffrey K. Liker identificeerde 14 kernprincipes in zijn boek, die de basis vormen voor “The Toyota Way”. Deze principes, zoals het nastreven van een langetermijnvisie, het elimineren van verspilling en het excelleren van mensen, verklaren het succes van Toyota. De Toyota Way benadrukt een technisch-sociaal systeem dat afhankelijk is van mensen en dagelijkse teaminzet bij probleemoplossing en verbetering. Wetenschappelijk denken wordt gestimuleerd om de vaardigheden van probleemoplossers te ontwikkelen.
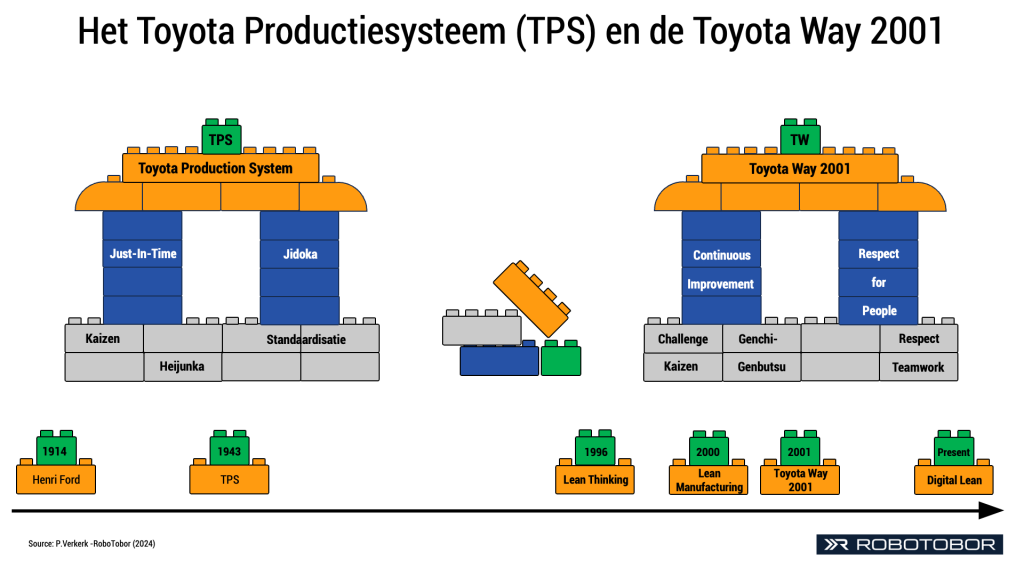
De 14 kernprincipes van ‘The Toyota Way
- Langetermijn systeemdenken – filosofie
- Verbinding van mensen en processen – creëer een continu-flow met toegevoegde waarde
- Een PULL systeem – voorkom overproductie
- Verdeel het werkvolume – Balans tussen productieaantallen en productiemix (Heijunka)
- Continue verbetering – werk aan processen
- Gestandaardiseerde Taken – kwaliteitsborging en continu verbeteren
- Symbolen en Visuele Hulpmiddelen – besluitvorming in werkprocessen
- Betrouwbare Technologie – een stapsgewijs doordachte aanpak
- Leiderschapsontwikkeling – cultuurversterking binnen organisaties
- Ontwikkeling Teamprestaties – bedrijfscultuur
- Respecteer zakelijke partners – groei en werk samen
- Observeren en Iteratief leren – wetenschappelijk denken en leren (Genchi genbutsu)
- Gezamenlijke Doelbepaling – continue verbetering en reflectie in organisaties
- Strategische uniek – uitvoering
De Just-In-Time (JIT)-pijler: Principes en fundamenten
Just-In-Time (JIT) is de eerste pilaar van het Toyota Production System (TPS) en richt zich om het produceren van diensten, goederen en materialen van de juiste kwaliteit en hoeveelheid op het exacte moment van de behoefte. Het hoofddoel is het vermijden van verspilling en het bevorderen van een efficiënte stroom van materialen en informatie naar het gebruikspunt. Een succesvolle implementatie van JIT vereist het opbouwen van sterke relaties met leveranciers, het handhaven van een stabiel werkschema en de actieve betrokkenheid van alle belanghebbenden. JIT strekt zich uit over alle fasen van de productieketen, van de levering van grondstoffen door externe leveranciers tot de interne stappen in de productiestroom die worden geleverd aan de volgende productiefase en uiteindelijk aan de klant. JIT omvat PULL, Flow en Takt. PULL wordt geïmplementeerd via een Kanban-systeem, waarbij onderdelen op een geautomatiseerde real-time manier worden aangevuld en minimale voorraden worden gehandhaafd.
De impact van Just-In-Time (JIT) op Autonome Mobiele Robot Systemen
In veel van mijn gesprekken over mobiele robots kwam vaak een “oh ja” moment naar voren. Het werd al snel duidelijk dat er nog werk verzet moest worden voordat een AGV- of AMR-project kon beginnen. Vaak was de ‘material flow’ niet volledig bekend of lag de focus op het moeilijkste intra-logistieke traject in de lay-out. Een eerste kleine pilot biedt meestal de beste inzichten en ervaring voor een groter tweede project.
Op het eerste gezicht lijkt Just-In-Time (JIT) niet direct gerelateerd te zijn aan een mobiel robotsysteem. De werkelijkheid is echter anders! Een JIT-strategie komt terug in vele ontwerponderdelen van het mobiele robotsysteem, zoals:
- De cyclustijden van machines en de snelheid van het inbound, outbound of marshalling-gebied. Al deze componenten hebben invloed op het ontwerp van de lay-out.
- De technologie en methode waarmee transportopdrachten worden gegenereerd: gebeurt dit automatisch of via menselijk handelen?
- Statische berekeningen en/of simulaties van het mobiele robotsysteem: met welke rij- en handelingstijden wordt er rekening gehouden? En zijn er verwachte vertragingen in de lay-out, hoeveel en hoe lang?
- De dispatching-algoritmes van de technologieleverancier. Dit is ook een lastig component om te traceren als mogelijke ‘root cause’ wanneer ladingen niet meer Just-In-Time aankomen of worden opgehaald.
Als de AMR-integrator niet de juiste vragen stelt over de material flow of jullie processen, kan de JIT-materiaal flow fout gaan. Wie zit er aan de andere kant van de tafel: een productverkoper of een intralogistiek expert? Als je hulp nodig hebt bij het selecteren van een AGV/AMR-leverancier, kun je mij inschakelen voor advies, begeleiding of af en toe brainstormen.
Hulp nodig met robotisering?
De stap naar robotisering kan overweldigend zijn, daarom sta ik klaar om jou te helpen!
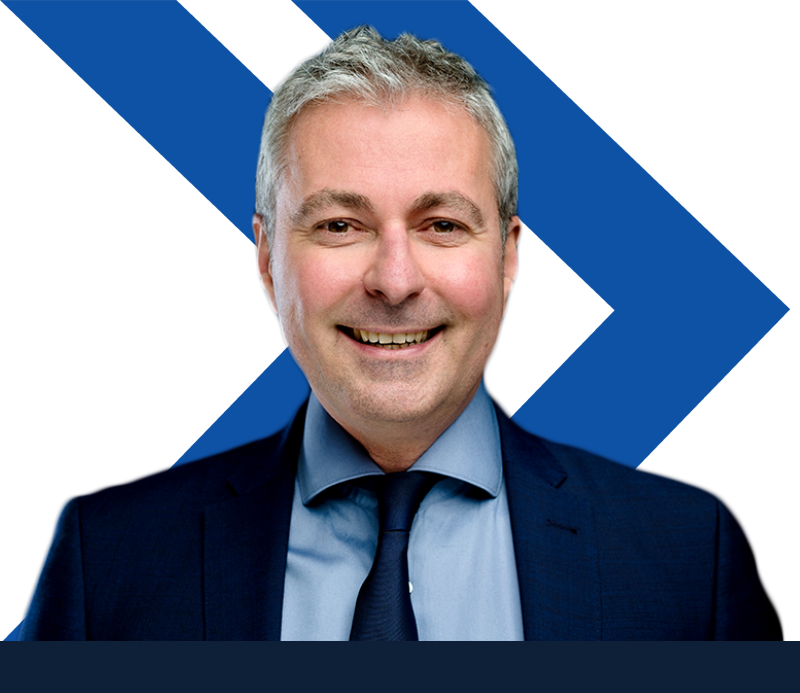
De JIDOKA-Pijler: intelligente Automatisering met een mensgerichte aanpak
De JIDOKA-pijler vormt de tweede pijler van het Toyota Productiesysteem (TPS) en richt zich op het ontwerpen van productieapparatuur die snel problemen in het gehele productieproces kan identificeren en corrigeren, met als doel defecte producten te voorkomen. Jidoka draait om slimme automatisering, waarbij machines taken uitvoeren en mensen verantwoordelijk zijn voor het detecteren van fouten.
Het ontwerp maakt het mogelijk voor medewerkers om de productielijn op elk moment te stoppen door ‘aan het Andon-koord te trekken’ of op een Andon-knop te drukken. Informatie wordt naar het “Andon”-display gestuurd om snelle probleemoplossingen te ondersteunen. Deze benadering leidt tot geautomatiseerde processen en machines die automatisch problemen detecteren en veilig stoppen, waardoor inspecties en indien nodig aanpassingen mogelijk zijn.
Zo draagt het systeem bij aan het voorkomen van herhaling van problemen, wat resulteert in behoud van kwaliteit en hoge productiviteit. De Japanse vertaling van Jidoka betekent “automatisering met een menselijke maat” of “intelligente automatisering”, wat het mensgerichte karakter van deze aanpak benadrukt.
JIDOKA en LEAN succesvol toepassen in AGV- en AMR-systemen
De keuze van een leverancier met in-depth kennis van intralogistiek en LEAN is van cruciaal belang voor het succes van een robotiseringsproject. Helpt de integrator bijvoorbeeld met het verwerken van de AGV/AMR vlootmanagementsoftware foutmeldingen naar jouw productiesysteem? Een foutcode die naar een handleiding verwijst, is niet meer van deze tijd. Voor Jidoka is een realtime foutmeldingssysteem van belang voor het continu verbeteren van het mobiele robotsysteem. Staat er een pallet, doos of ander obstakel in de lay-out en hindert dat de systeem perfomance?
Hoe fijn is het dan dat er een melding komt en dit verholpen kan worden. Zijn jouw medewerkers ook met LEAN/ Jidoka opgegroeid, dan worden problemen snel gedetecteerd en opgelost, en worden processen aangepast om herhaling te voorkomen.
Heijunka: Balans en Stroomlijn in de Productie
Heijunka vormt de kern van het Toyota Production System (TPS). Het richt zich op het gelijkmatig verdelen en ordenen van producten naar een productielijn of cel. Het doel is een stabiele productiestroom creëren en onregelmatigheden en overbelasting verminderen. Dit gebeurt door productievolumes en productmixen gelijkmatig over een periode te verdelen. Heijunka harmoniseert zowel het type als de hoeveelheid producten over een vastgestelde tijd, waardoor productie efficiënt aan klantvraag voldoet. Een belangrijk aspect is de continue aanvoer van productieorders, ondersteund door de Heijunka-box, een visueel hulpmiddel voor werkplanning. De Japanse vertaling, “het gladstrijken en op niveau brengen”, benadrukt de essentie van dit principe. Een praktisch voorbeeld van Heijunka is wanneer vijf producten X en vier producten Y in de productieplanning staan. Traditioneel zou de volgorde XXXXXYYYY zijn. Toyota past Heijunka toe door de productie te plannen als XYXYXYXYX, wat resulteert in een meer gebalanceerde productie.
LEAN Manufacturing
LEAN manufacturing is een methode die zich richt op het minimaliseren van verspilling in productiesystemen en het maximaliseren van productiviteit. Het gaat vooral om het reduceren van verspilling in processen om meer te kunnen focussen op waardecreatie. LEAN manufacturing verbetert efficiëntie, waardoor middelen kunnen worden vrijgemaakt om effectiever te zijn. Effectiviteit meet het vermogen om een gewenst resultaat te bereiken, terwijl efficiëntie meet hoe de laagste hoeveelheid middelen wordt gebruikt om de grootste output te produceren. Alles zonder toegevoegde waarde wordt beschouwd als afval. LEAN moedigt productiemanagers aan om tijd op de fabrieksvloer door te brengen, waar ze concrete verbeteringen kunnen doorvoeren, in plaats van de hele dag op kantoor te blijven. Dit sluit aan bij het Japanse woord “Gemba”, dat verwijst naar de plaats waar waarde wordt gecreëerd.
“Een Autonomous Mobile Robot (AMR) Systeem is doeltreffend wanneer het alle ladingdragers Just-In-Time (JIT) bij medewerkers in de assemblage plaatst. Aan de andere kant is een AMR-systeem pas efficiënt als het met minder kosten de ladingdragers kan transporteren dan wanneer medewerkers met handpallettrucks dit zouden doen.”
De vijf kernprincipes van LEAN manufacturing worden gedefinieerd als Waarde (Value), de Waardestroom, Flow, Pull en Perfectie.
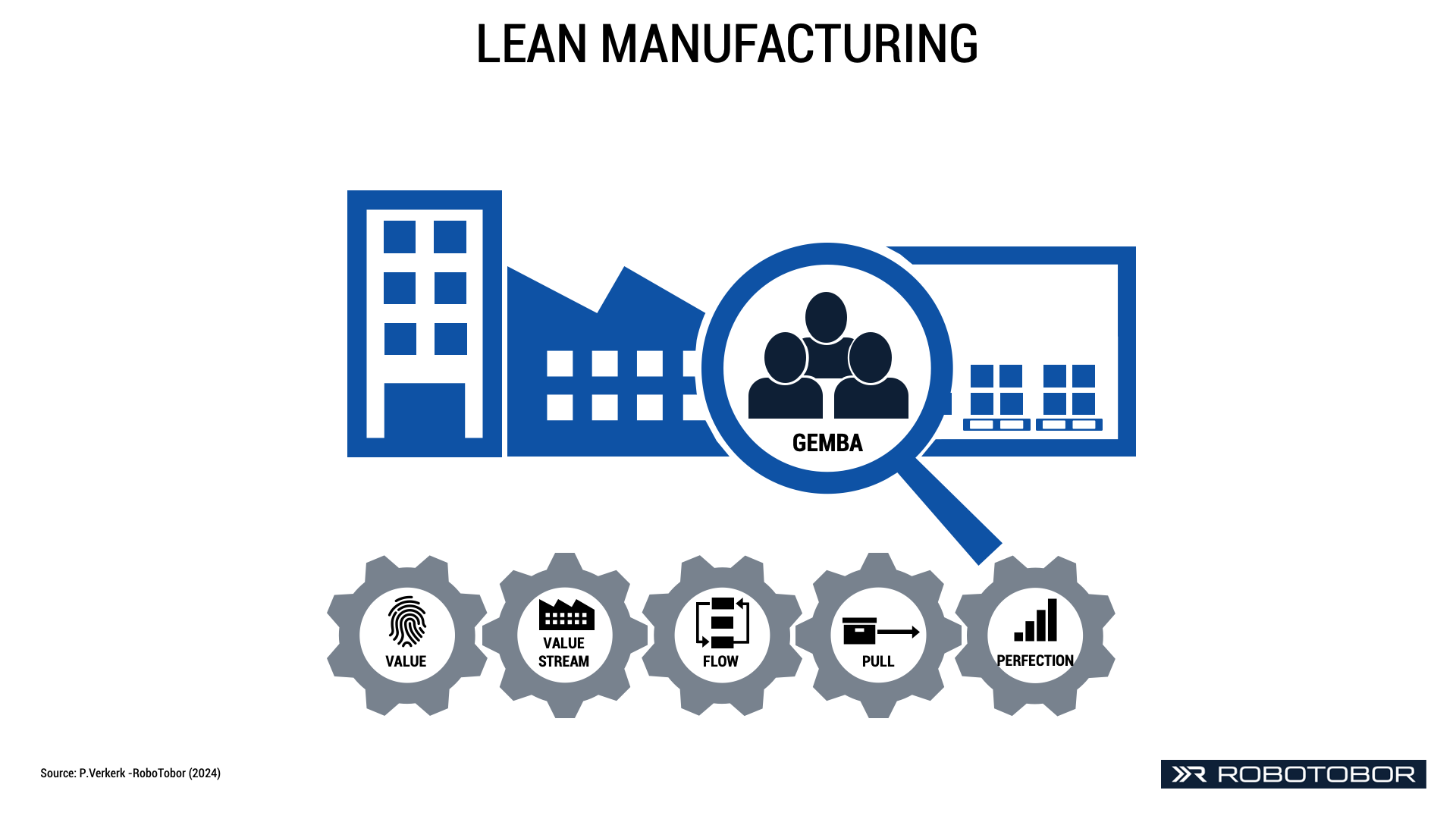
- Waarde: is dat waar de klant voor betaald – hij betaald voor iedere activiteit die door iedere werknemer wordt uitgevoerd.
- Waardestroom: value stream mapping is een methode die wordt gebruikt om activiteiten te identificeren die waarde creëren.
- Flow: waarde wordt niet in een moment gecreëerd, maar in een stroom (flow) van activiteiten.
- Pull: betrekt de klantvraag en minimaliseert de voorraad en dat vereist materiaalaanvulling op basis van het verbruik (Kanban).
- Perfectie: een toegewijde organisatie (team) met een mandaat om continu verbetering in de organisatie op te bouwen.
Wil je starten met LEAN Manufacturing voordat je gaat Robotiseren? Neem dan contact met me op!
Je wil gaan robotiseren? Dan kun je beginnen met Value Stream Mapping. Hiermee zet je een flowbril op en kom je op een snelle manier te weten wat de huidige toestand van je productieorganisatie of magazijn is. Value Stream Mapping is gemakkelijk zelf te doen, maar dan moet je wel weten waar je op moet letten. Voorkom de grootste Value Stream Mapping blunders en lees: Wil je beginnen met robotiseren? Ontdek eerst de kracht van Value Stream Mapping!
Copyright © 2024; Patrick Verkerk, RoboTobor